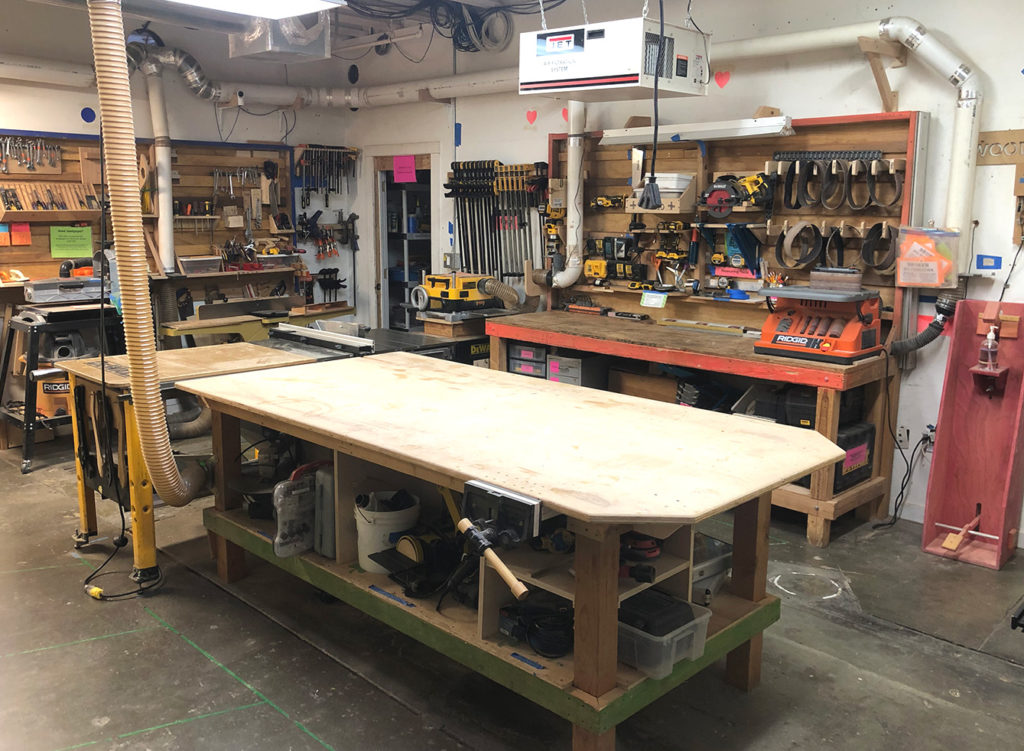
Every day we strive to create great experiences for everyone who walks through our doors- no matter where they are on their maker journey. Our inclusion-forward approach informs everything we do including how we design our spaces to welcome users across the skill spectrum. This is one of the many ways we take action to implement our mission in everything we do.
Relative to its small size, our shop houses an impressive collection of tools, workstations, and resources which presents unique challenges when it comes to usability and access for makers with diverse skill sets and experience levels. Finding sustainable solutions to address these challenges and create a great shop in which everyone can try new things, learn, grow, and share knowledge requires:
- Approaching problems from an explicitly inclusion-forward perspective
- Enthusiastically embracing change, innovation, and curiosity
- Pro-actively experimenting with solutions
- Seeking input, asking questions, and learning together as a community
- Engaging in responsive problem solving as community needs evolve
While some of the recent changes are more noticeable like new table tops and work surfaces others are more subtle like adding a side stop to our spindle sander to prevent creep during use. Each adjustment and/or repair big or small was made intentionally in response to community needs, observed patterns of use/breakdown, and bolstered by input from users of all skill levels.
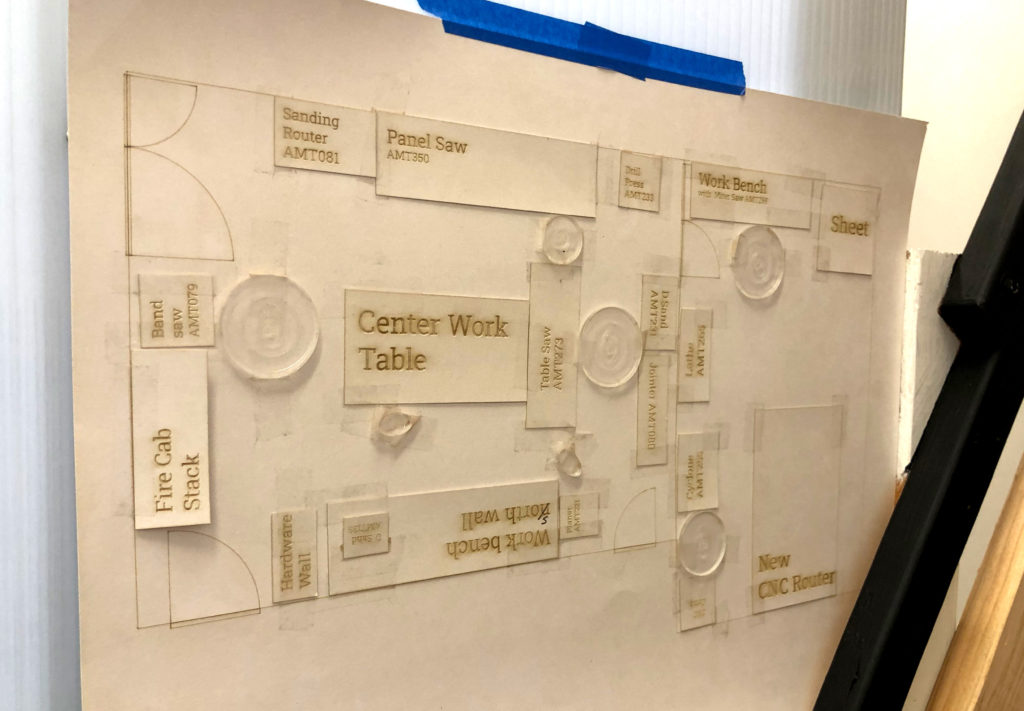
Optimizing Tool Use Space and Small Tool Storage
While our collective imagination is infinite, our space is limited… This reality was omnipresent during our recent project, the Great Tool Swap.
When it comes to using our shop we constantly negotiate overlapping “tool-use” spaces. In other words, where you stand to use tools like our table saw, drum sander, jointer, and planer blocks access to others and prevents concurrent use.
In order to maximize our tool-use space and maintain reasonable workflow we carefully examined how folks were using the shop, identified chokepoints, gathered feedback from the community, and ultimately decided to re-arrange our dust collection set-up and swap the locations of our drill press and bandsaw.
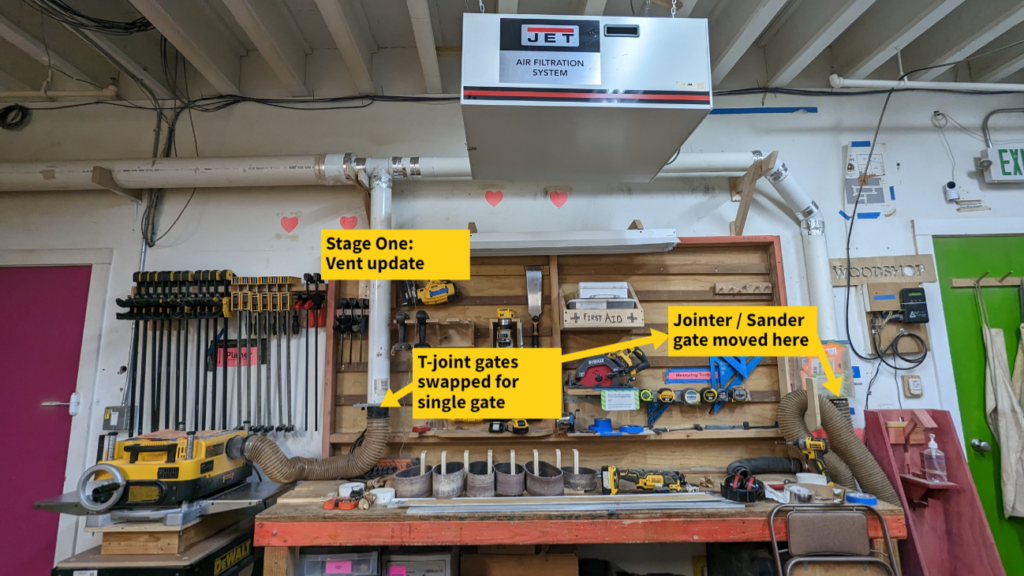
Beyond overlapping tool use spaces we also have limited storage for smaller tools and supplies like drill bits, saw blades, clamps, and gauges. Overly dense storage makes it hard for folks (especially beginners) to locate what they need and/or discover new tools. It’s also difficult to label dense storage effectively and for our community to keep it organized. By re-arranging vertical storage in the shop and finding new homes for small tools we were able to create a more user friendly visual system for tool storage.
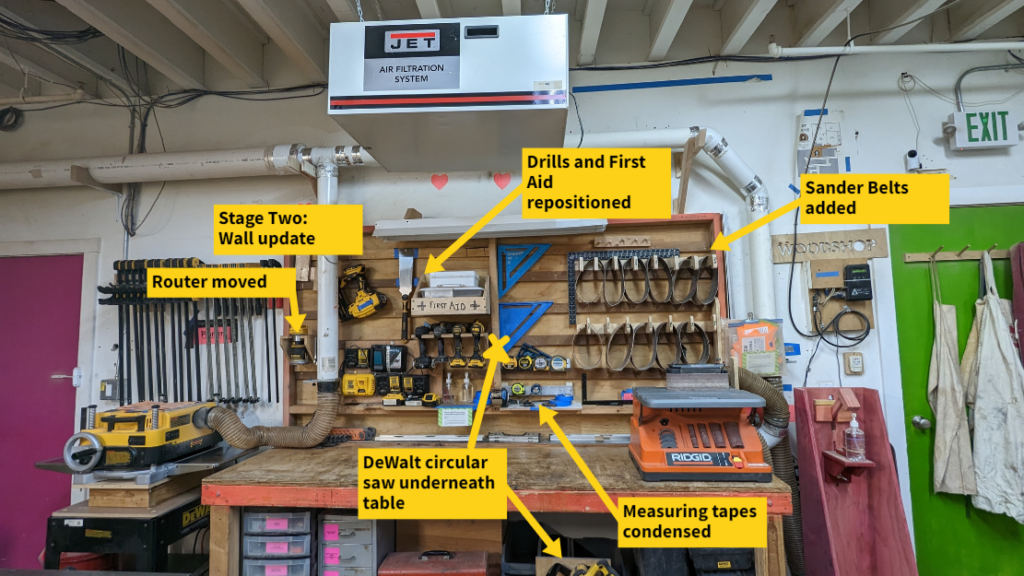
Embracing Entropy as an Invitation for Change
Permanent systems are a myth. Just because something has “always” been one way, does not mean it needs to stay that way.
Sometimes systems work in theory but not in practice, become less functional over time because needs for change, or fail to fully resolve underlying issues. Instead of seeking permanent solutions, we look for sustainable ones. For example, when looking holistically at the shop we realized we were stuck in a cycle of reactive Air Quality Management resulting in unpredictable and frustrating shop closures.
We wanted to move toward a more sustainable, predictable, and proactive system so we installed a new manometer, a meter that measures air pressure differences, to measure the draw of shop ventilation. We also added a convenient QR code that allows shop users to easily update our air quality logs. This small change has improved our ability to track filter life and stay ahead of maintenance.
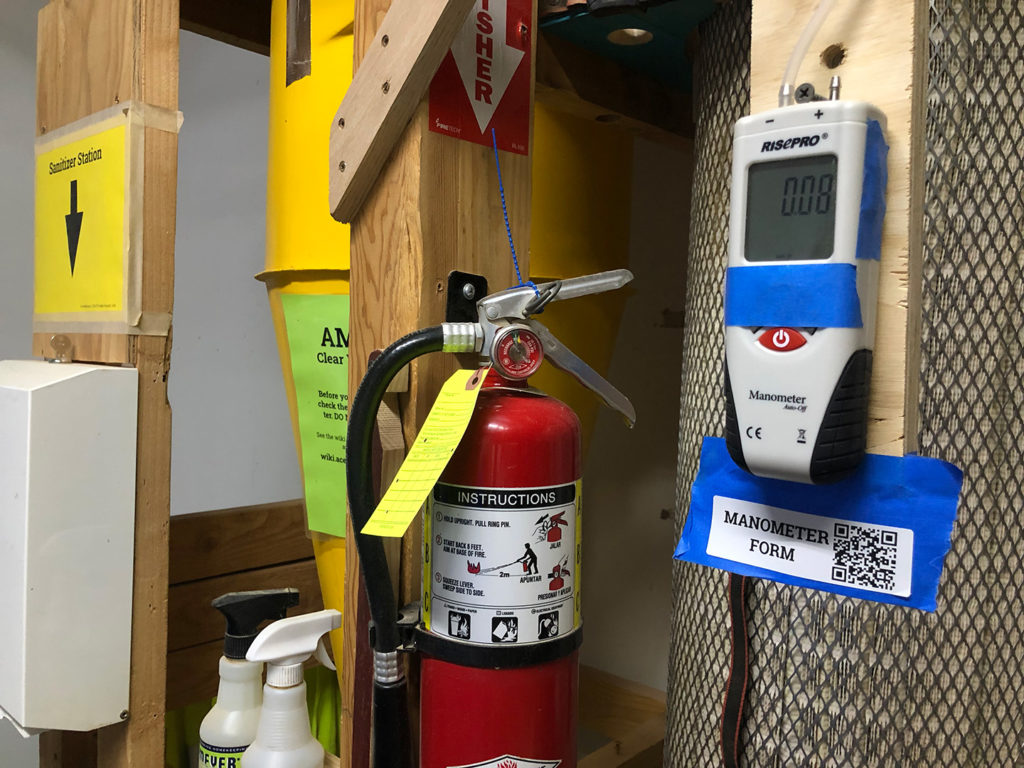
The Power of User Input
Expertise is valuable but it’s not the whole story when it comes to designing a shared workshop for the Ace Members we serve. Systems that might work for advanced users can discourage new users and/or put up barriers to access. Experienced users may notice issues that new users may not, but resolving those issues requires input and participation from beginners to be effective.
Relying on a narrow “expert is best” framework is also counter-productive to inclusive shop design because it can reproduce the systems of privilege and power that have limited who is normalized in technical spaces. Instead, we include the perspectives of new users as “expert” especially when it comes to navigating the workshop as a beginner.
For example, we learned specifically from new users that they were struggling to identify and find what they needed in the shop making starting out feel intimidating and overwhelming. To better welcome them we added more labels to our tools. We also created two Shop Basics and Tool Overview classes to better demystify shop etiquette and help new folks get oriented.
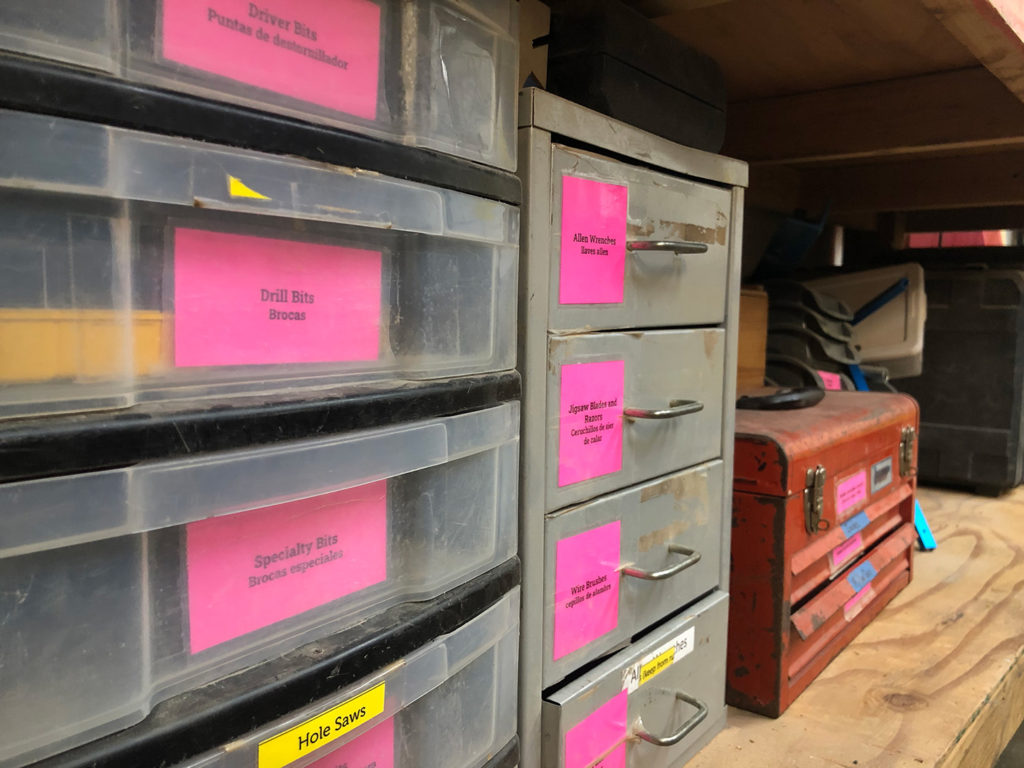
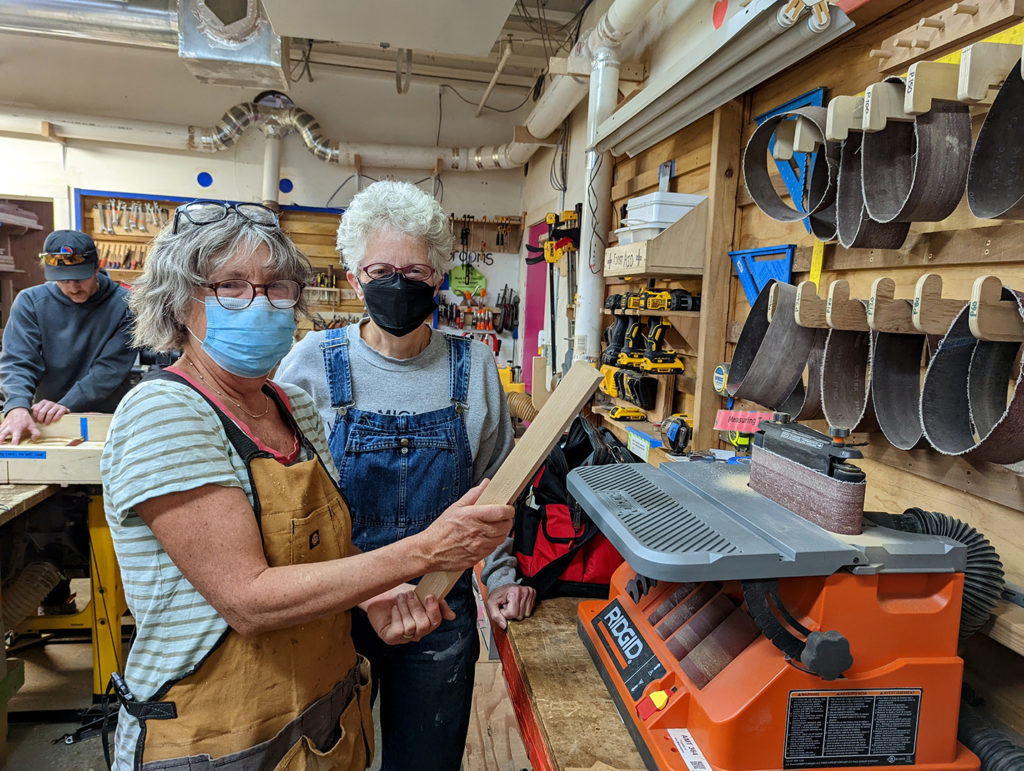
And the Beat Goes On
Our community is always changing and our spaces need to keep pace with those changes in order to best serve everyone. Through our inclusion-forward approach to design, we ensure that the changes we make are more effective for everyone who walks through our shop doors.
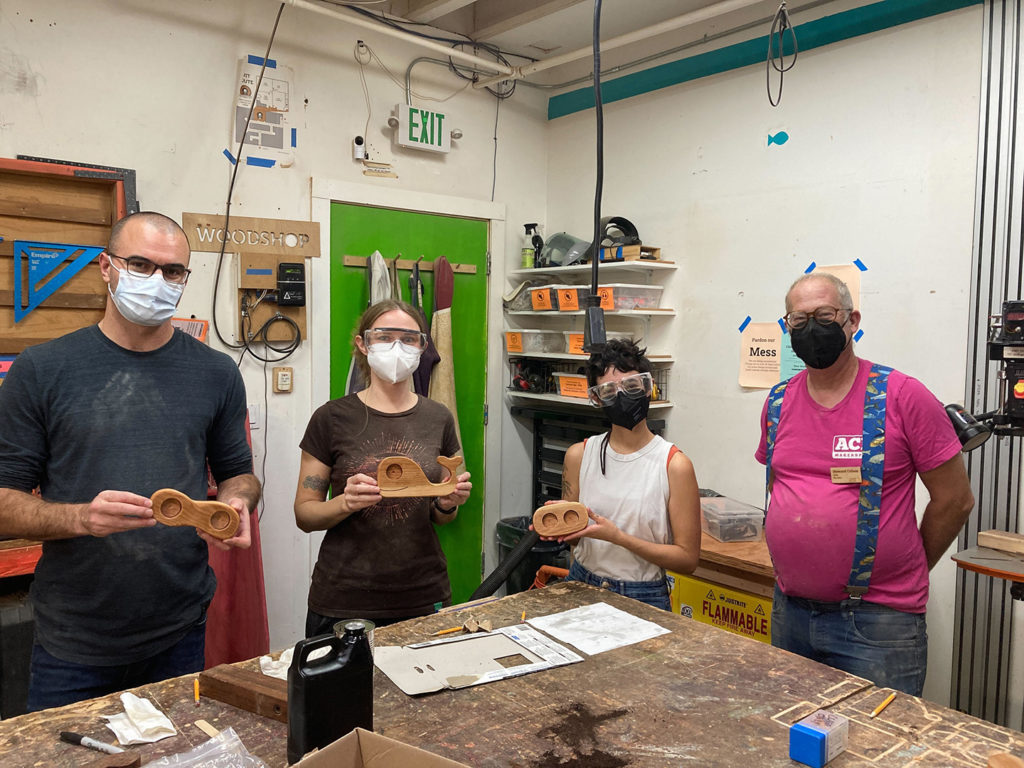
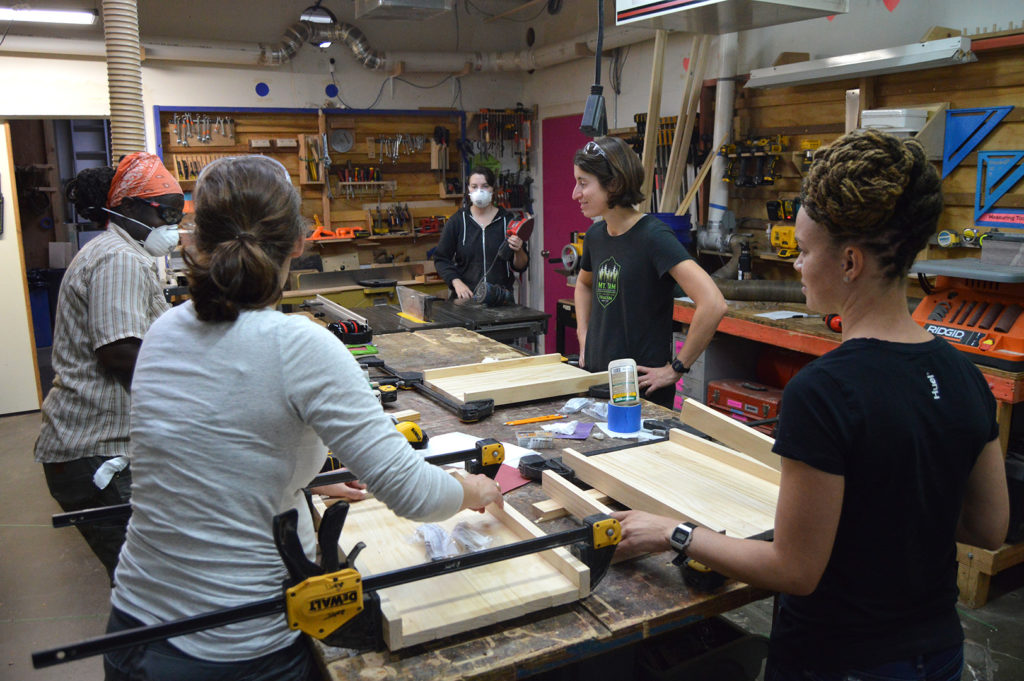